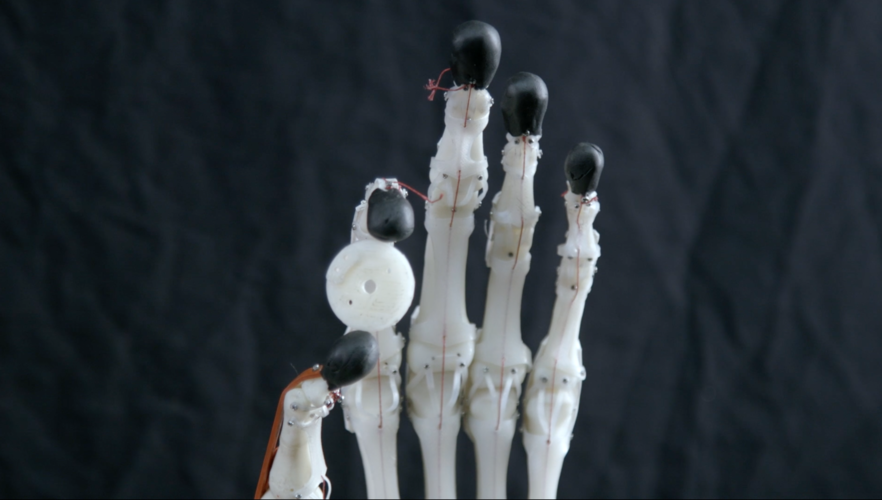
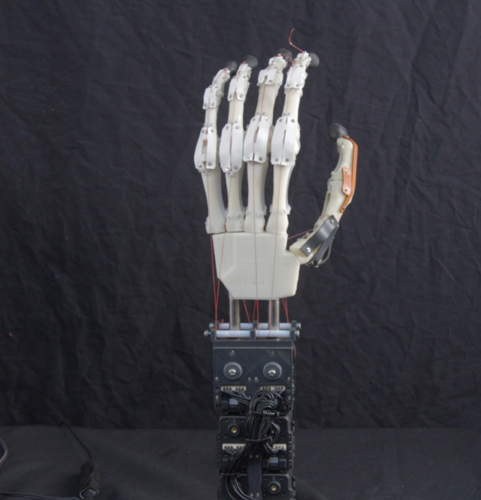
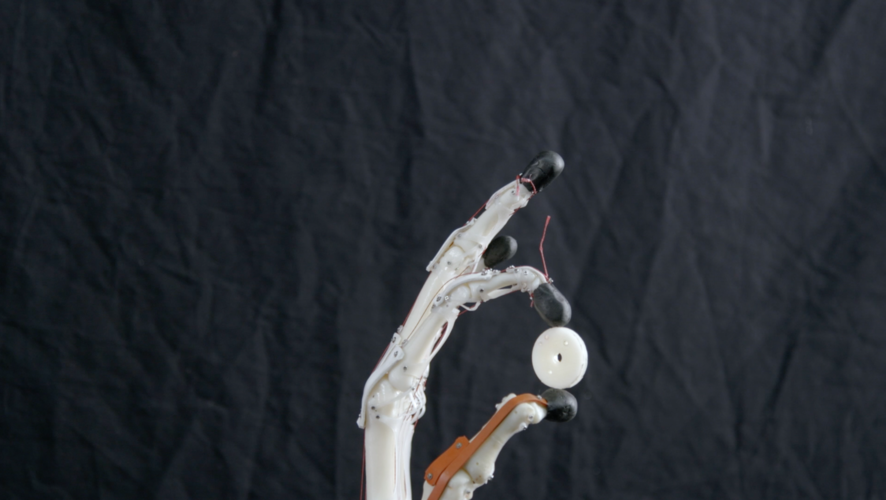
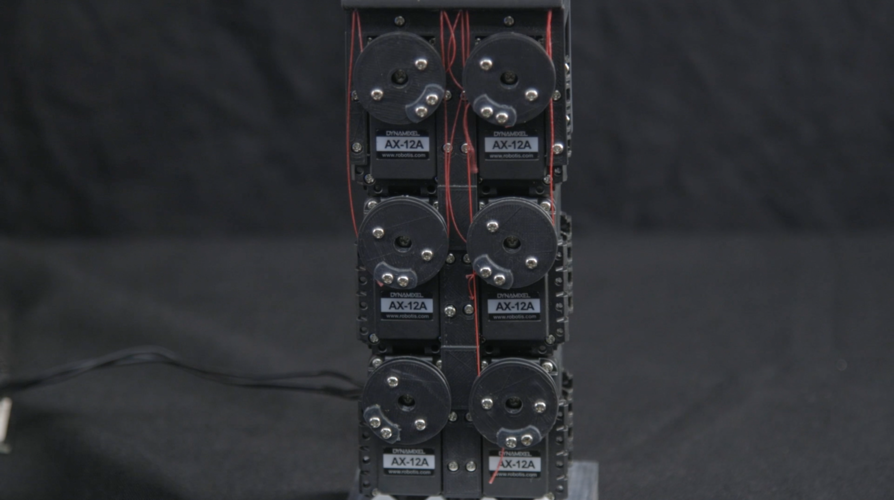
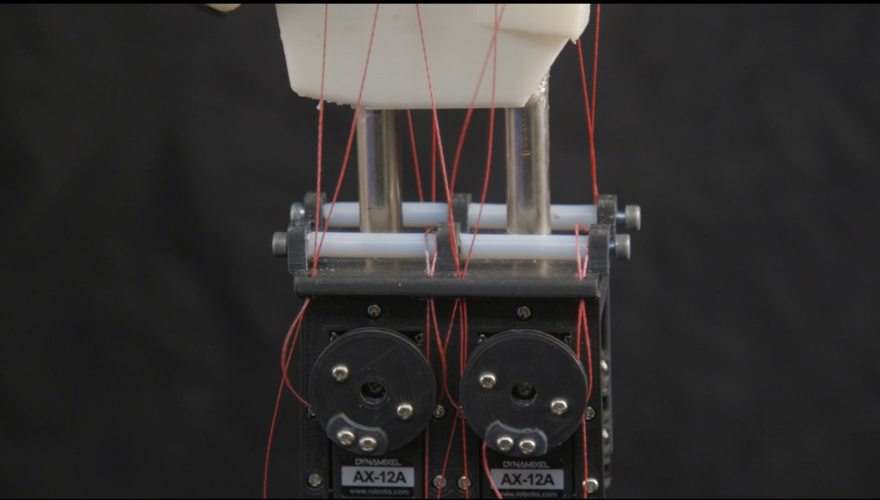
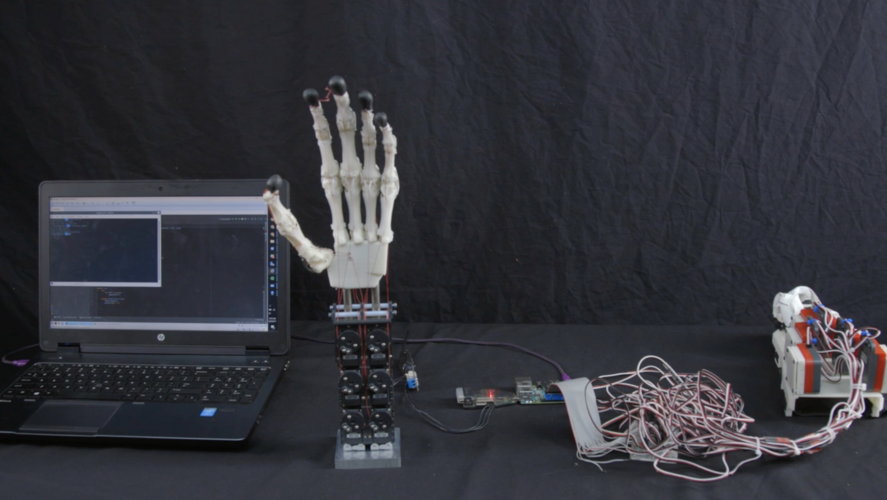
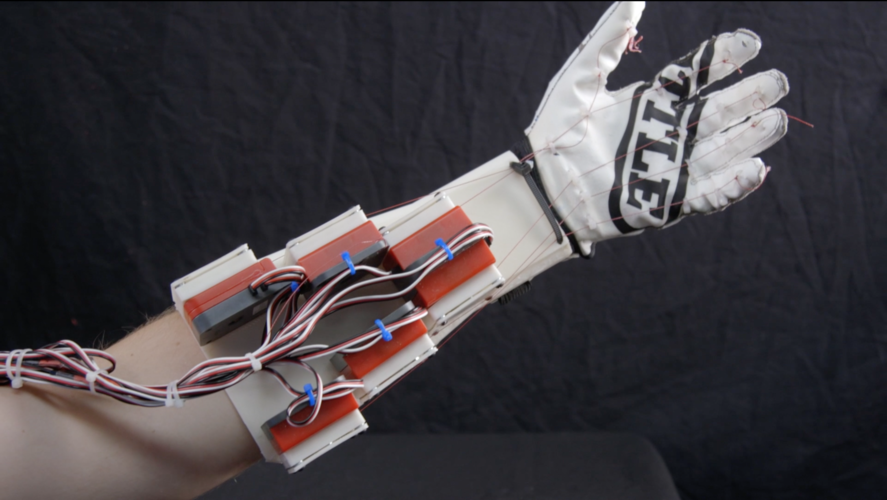
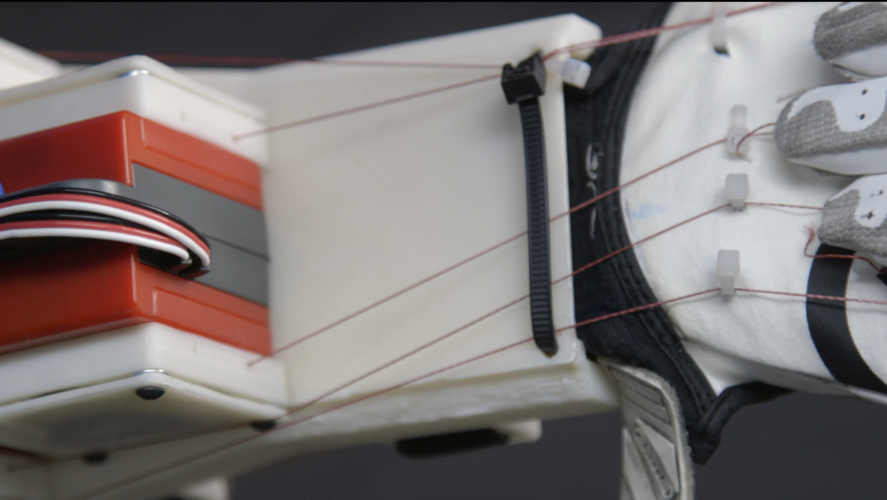
Prints (0)
-
No Prints Yet
Be the first to upload a Print for this Design!
Description
My project is a 3D printed biomimetic robotic prosthetic hand. It is comprised of 3D printed bones, ligaments, tendon sheaths, and supporting structures like the palm and servo tower mounting pieces. In addition, I take advantage of both rigid and flexible materials in my design. The bones and mounting hardware are made of ABS, and the ligaments and tendon sheaths are made from Taulman 3D’s PCTPE filament. The tendons for my hand are made of spectra deep sea fishing line. I have been working on the hardware for this project for 10 months now, and it's comprised of 54 different stl files - 20 bones, 14 tendon sheaths, 16 ligaments, 20 tendon guides, 1 palm, 2 servo mounting plates, 6 pulleys, and 1 carpal tunnel. I designed 37 of the 57 unique 3D files for the project. The other 20 are bone files that have been highly modified from the original files to fit my project. The base files before all my changes can be found here: http://www.thingiverse.com/thing:15342
My design innovates on the current state of robot hands in several way, but the most significant is that takes advantage of biomechanics to achieve a higher level of dexterity. My design incorporates the major components of the human hand (bones, ligaments, tendons, tendon sheath, intrinsic muscle) which allows my hand to have human like movement and speed. Instead of using traditional mechanical joints, I followed the blueprint of the human hand, using printed ligaments and laser cut rubber to form a joint capsule, which has had it rewards in terms of performance and improved dexterity over traditional robot hands.
The next way my design innovates is in the control department. Since my design closely parallels its human counterpart, I can use existing data from how the human hand moves to control the hand. Instead of writing completely new code to control my hand, all I need to do is track my actual hands movement with draw wire sensors and send that data over to the hand. My design makes the software side of this project significantly less complicated
While the actual hand in my project is larger than human scale because of ease of manufacturing, the form factor of my servo motors to control the hand is very similar to the size of my forearm which is the part that the servo array is mimicking. Most robot hands are more bulky, so my design is innovative because of its smaller and more manageable form factor.
Finally, my last design innovation is reducing cost. Since most of the design can be printed on a hobbyist 3D printer, the overall cost of the project including motors and other parts can be kept under $600. This is a huge improvement when compared against other prosthetic hands, and an even bigger improvement when compared to other robot hands that try to mimic biomechanics. The level of detail and customization of this hand would make it much more expensive to manufacture if I did not have a 3D printer. Also, all of the parts can be printed in about 2 days, if you are printing through the nights.
Fun Facts:
Each finger has 46 screws, 8 washers, 3 tendon sheaths, 3 ligaments, 4 bones, 1 finger tip, 3 pieces of laser cut rubber, 2 tendon guides, and 2 lengths of fishing line for the tendons.
It takes about 45 minutes to build one finger
Most parts were printed on an Ultimaker 2 with an E3D extrusion upgrade kit
Note: This project is inspired from the research paper below. I have modified some design elements, but credit is due to the brilliant researchers who wrote the paper below.
Research paper link: https://homes.cs.washington.edu/~todorov/papers/XuICRA16.pdf
Progress videos:
My blog: ggalisky.weebly.com
Comments