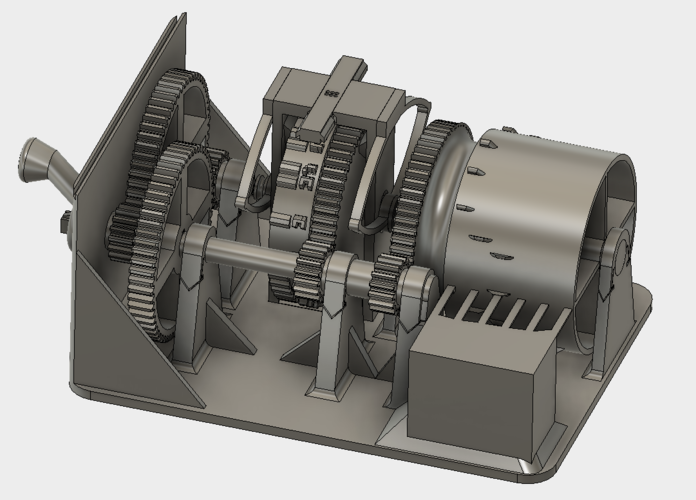
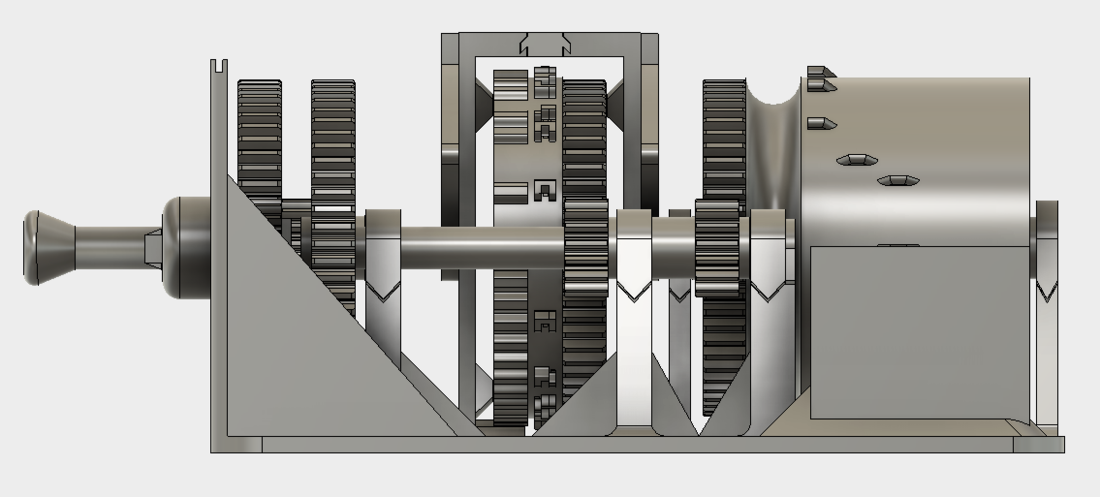
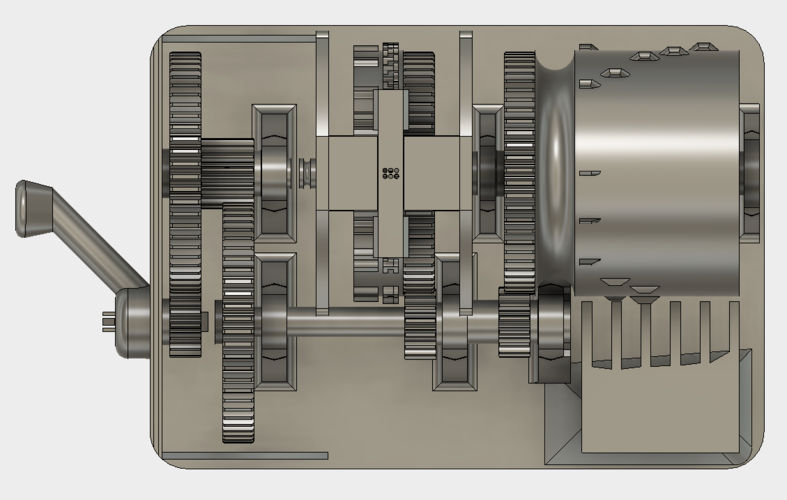
Prints (0)
-
No Prints Yet
Be the first to upload a Print for this Design!
Description
Concept
I can still hear my piano teacher, Mrs. Wentz, singing along as she called out the notes. "No you got that wrong, it goes like this," and she'd sing, "A, C, B, B, G," Hearing the notes as I watched it on the sheet music was just what I needed to understand how the song was supposed to be played
How does that work for visually impaired music students reading music braille? Even though they know what a quarter note, sixteenth note, and half note should sound like, sometimes stringing it all together can get confusing. Having someone sing or play the rhythm as you see the notes on the page is invaluable. If you're reading braille music, how do you coordinate your hand with their voice? Or how would a beginner make the connection between what they read, and what they hear? Wouldn't it be great if as the music was playing, the braille would play along with it? Sound and touch, together as one.
As you crank the shaft of this box, a familiar song plays. Put your finger on the pad on the top of the box, and you can follow along in music braille. The Braille Music Box is perfect for an introduction into music braille.
Development
The first task at hand was trying to make music. I went through quite a few iterations of prongs, varying the length, thickness, width, and spacing of the prongs. I also added different "weights" to the tips of the prongs to note the effects of pitch changes. After playing around with box sizes and then boxes with holes vs boxes without holes, I settled on the final design. Some of the iterations are shown here:
From these music box tests, I also determined that in order to get the cleanest sound possible, the joint between the music box resting surface needed to be a rigid as possible. All attempts at snapping together the box resulted in "fuzzy" notes, therefore, I chose to use superglue to secure the music box to the frame.
Once the music box design was finalized and tuned correctly, I started designing the music drum. The design of the drum pins are non-traditional. This was driven by the fact that I wanted the drum to be able to be printed without any support material.
The next challenge I recognized was the braille mechanism. The braille mechanism had to do two things: indicate the correct music braille note, and play it in time with the music box. Instead of simply inscribing braille on the perimeter of a drum and having it pass over your fingers, I wanted the braille to "pop" up from a single pad. I realized very early that I wouldn't be able to simply slide the braille drum over the braille pins because while it's engaging and disengaging the pins, it could confuse the reader. This meant that the drum indicating what note was playing had to move up and down as the music played. You can see some of the different versions here:
I chose a cam type mechanism and played around with a few different profiles until the motion looked right. I think the next iteration will be a linkage type mechanism to increase the fluidity of the movement. You can see different iterations here:
The final task at hand was increasing the output torque enough to drive both the braille drum and the music drum. This played well with the fact that I wanted the music to be relatively slow so that the braille reader would have time to recognize the notes as they popped up through the interface. I first determined how fast I thought a typical user would crank the input shaft (approximately 100 RPM). Next I determined what a comfortable reading speed would be for the user (approximately 7 RPM). With those two numbers, I calculated the required gear ratios while also keeping the diameters of the gears at a reasonable diameter.
Measuring in at 250 x 180 x 130 [mm], this is definitely not a pocket-sized music box. The size was mostly driven by the braille mechanism, as it needed to fit the entire song along it's perimeter. Another driver of the large size, was the music box itself. Prong dimensions along with note spacing resulted in a large drum.
All pieces were designed to minimize the use of support material. Every part, with the exception of the music box, snaps together and does not require gluing (see "Issues" section below). The correct print orientation for each part is crucial for smooth assembly and operation. The layer lines for all snap fit parts are oriented for maximum strength. Where possible, the sliding contact joints have the same layer line orientation. Originally I planned on making the shaft supports modular so that their layer line orientation would be the same as the shafts, but that left the potential for misalignment of the shaft supports. I chose to print the entire bottom frame in one piece to guarantee correct shaft alignment.
Design Notes:
You can find all my notes that I used during the design process below:
Final Thoughts
This marks the first version of my printable braille enabled music box. The future versions will have several improvements, including a smoother braille indicating motion, an overall reduction in size, and a modular song design that would allow a user to change the song. Furthermore, the design will be optimized for printing on a wide range of 3D printers, and indicating marks for easier assembly will be included.
This object was designed to be printed with my specific printer (Prusa i3 MK3) and filament (Hatchbox PLA). Due to differences in printers, and filaments, certain aspects of this design (sliding contact joints, gear meshes, snap fits etc.) may not perform as shown here. Filament settings are highly adjusted for each specific part. I will soon upload all settings for every part.
Issues:
The braille drum was designed to be driven a certain direction, so as to help it over the cam. After printing off the music drum, I realized that I modeled the song backwards to the movement of the braille drum. Because of this, with my printed model, you have to run the music box backwards to hear the song correctly and forward to read the song in braille correctly. I would have re-printed it, but I ran out of time. The supplied model for the music drum is the correct orientation.
The cover for the model was also omitted because of time constraints. The cover is meant to include the Braille Hub frame, as well as the springs. Since the cover is omitted, it is required to superglue to frame and springs together.
Comments