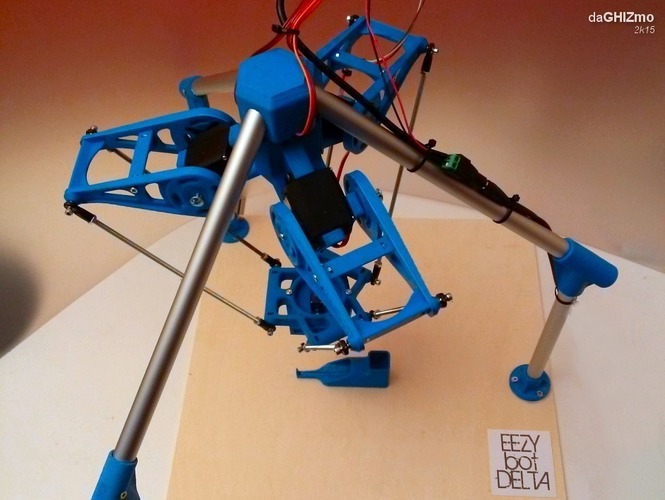
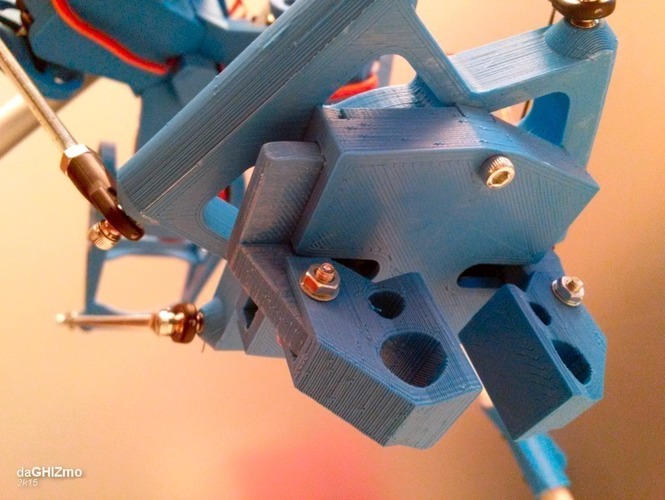
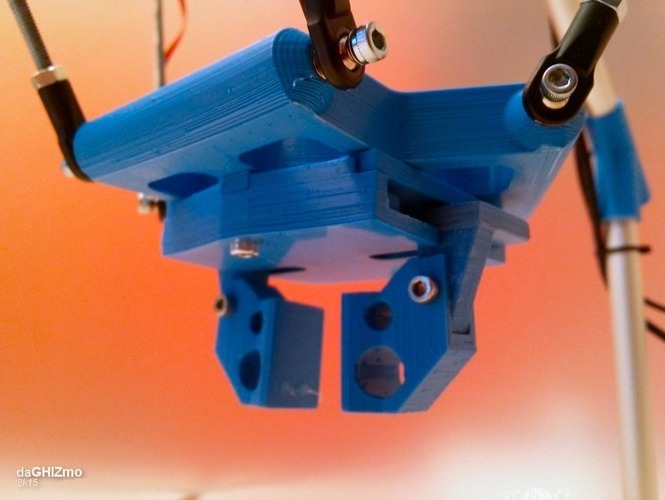
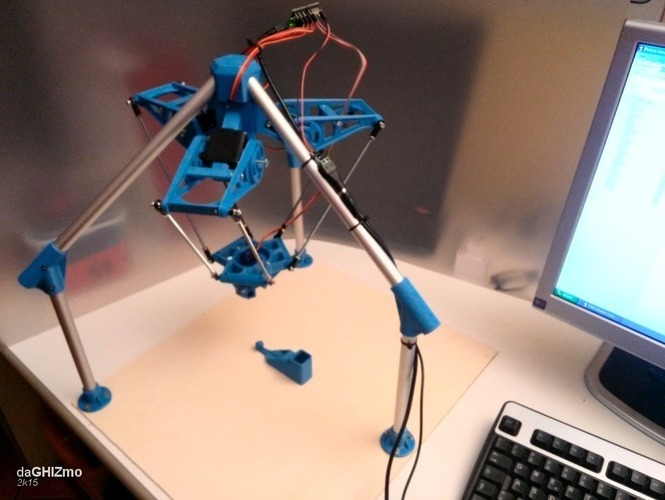
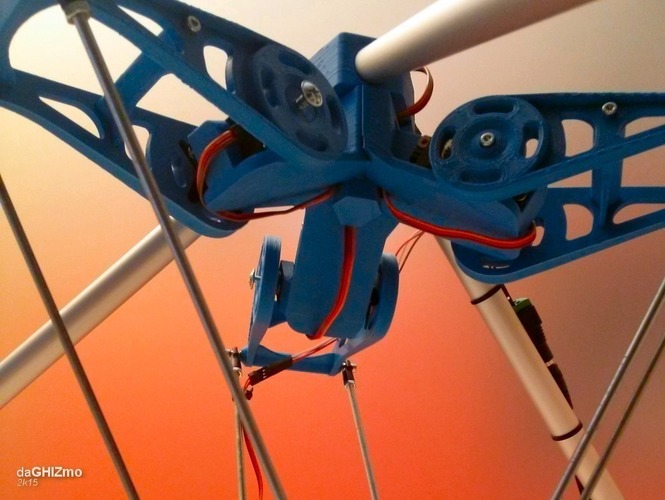
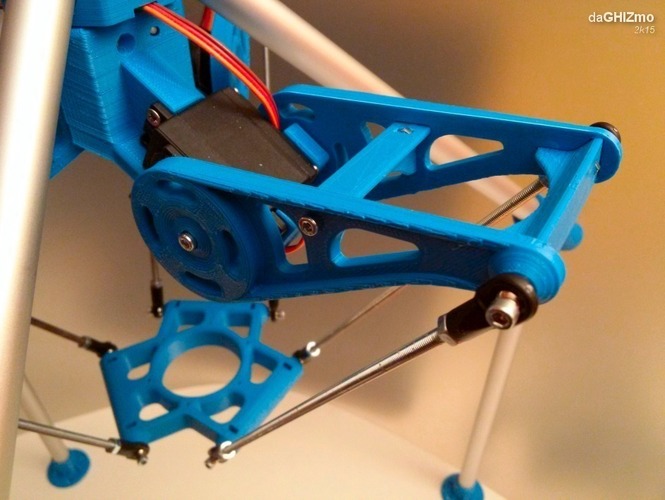
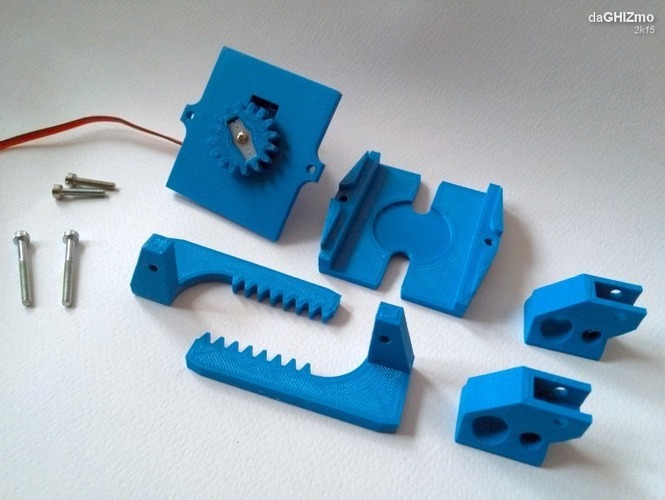
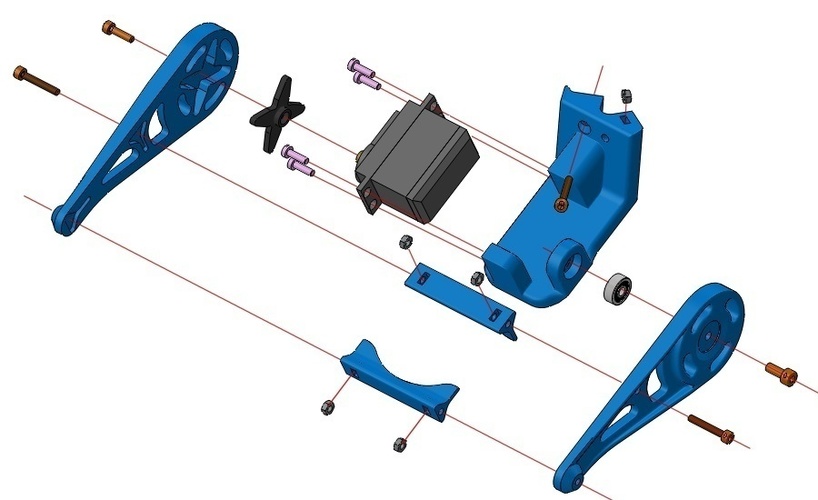
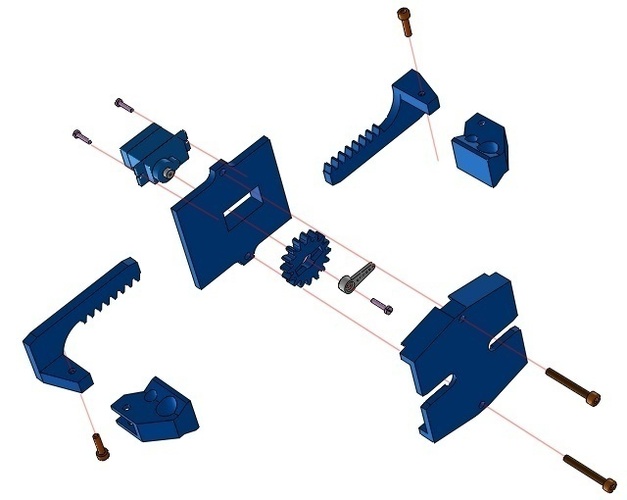
Prints (0)
-
No Prints Yet
Be the first to upload a Print for this Design!
Description
SummaryI've always been fascinated by the world of robots since I was a kid, especially I would like to make and watch them move. Now through 3D printing I have finally the power to make this happen; I can design them, print the parts, assembly them and animate. So after EEZYbotARM .... EEZYbotDELTA ( 2 pass the ball 2 :-) ) Following the aims of my previous robot arm http://www.thingiverse.com/thing:1015238 I developed a second one. This one belongs to the family of "spider" Delta robots. In industrial applications it is mainly used for assembly purposes (Pick and Place) videos: https://youtu.be/mR6eCmtux_g https://youtu.be/oGUTnrtlgHw 24/01/16 new video about controlling the bot via bluetooth an smartphone https://youtu.be/TCjfZnsRWU4 code and app free http://www.instructables.com/id/Android-APP-to-Control-a-3DPrinted-Robot/ Delta bots have the advantage that they have common parts for all the driving items (normally 3 or 4) thats simplify the construction. I try to follow the philosophy of my previous thing that must be: small, cheap and easy to assemble but this time I had to use bigger servo (mg995) for the three main arms so this makes it a little bigger ( 400 x 450 x 450h mm of occupied volume comprehensive of structure). http://www.servodatabase.com/servo/towerpro/mg995 I kept a smaller sg90 servo for the gripper. http://www.servodatabase.com/servo/towerpro/sg90 I have added also a structure to hang up the main body. It is a mixed construction and is made with printed parts, and Ø16 mm aluminum pipes that I get from a local hardware store. This is a ready-made solution, but you can make your own. Also in this case I made a printed ramp to make an handling "demo loop" that can be watched in videos. for the assembly have a look at my instructable here: http://www.instructables.com/id/EEZYbotDELTA-3Dprinted-Robot/ COMMERCIAL ITEMS BOM (I use metric hardware) n°3 MG995 servo n°1 sg90s servo n°3 604zz ball bearing n°12 Uniball Traxxas M4x17 Crawler/Scaler ... (bought on ebay) n°3 Ø16 x 1 l=220 mm aluminum pipes n°3 Ø16 x 1 l=330 mm aluminum pipes n° 6 M4 x 200 mm long threaded rods n°15 M3 nuts n°6 M3 x 14 TCEI screw (receessed hex head) n°6 M3 x 20 TCEI screw (receessed hex head) n°6 3x15 self tapping screw n1 400 x 450 mm plywood sheet ELECTRONICS Like already explained in my previous robot arm, there are several ways to control it but I do not want to provide ready made solution. The purpouse is just that, produce a sufficiently reliable and ready hardware to allow users to explore they own way to control it. In any case if you are, like me, alien for what concerns the electronic parts, and you need the fastest and easyest way to obtain results in controlling the bot, I suggest the Pololu Mini Maestro card. https://www.pololu.com/product/1352 The card is provided with a free downlodable software that give you the power to drive with an easy grafical interface all the servos moving manually slides. In the mean time you are able to set the values of speed and acceleration for any singular item. You can also build sequences of commands in a easy way, store them in the controller o get the code automatically.Print SettingsPrinter Brand: RepRapPrinter: PRUSA i3Rafts: Doesn't MatterSupports: NoNotes: printed in ABS when I get time also this time I'll made an instructables for the assembly -> 01/02/16 made! 18/01/16 Udated EBD.01.01.002_R01 mast.stl improved for a clean wire installation
Comments