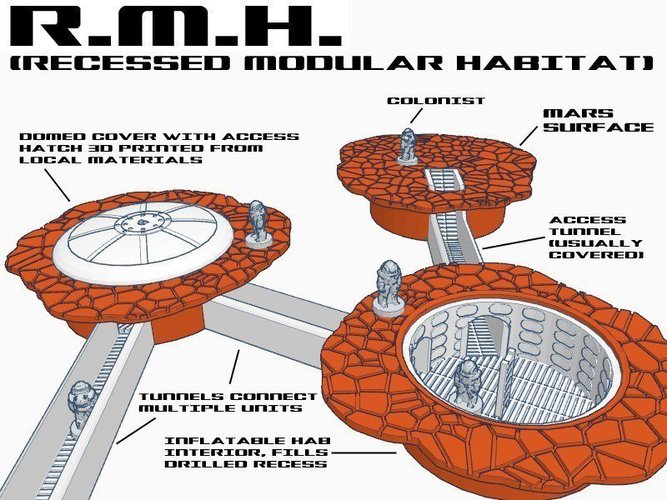
Prints (0)
-
No Prints Yet
Be the first to upload a Print for this Design!
Description
Summary The Recessed Modular Habitat is designed to utilize the greatest amount of material resources natively available on Mars, in order to minimize the supplies to be transported, thus minimizing cost. There are a number of primary concerns that must be addressed when planning a long-term mission to a hostile environment; the most obvious of these are the need for water, air, and food. Secondary concerns are related mainly to the specific environment that we are focusing on, and include temperature control, the ability to generate non fuel-derived power, and providing for some defense against the intense weather experienced on the surface of the planet. We will discuss proposed solutions to these concerns, each in turn, in the outline below. The proposed mission would take place in two phases, comprising two separate launches, approximately two years apart, to coincide with optimal Martian launch windows. During Phase 1, the first rocket would carry equipment, a load of elemental sodium, potassium nitrate, communications equipment, and a set of five robots. A landing site would be chosen to satisfy the overlap of two basic conditions: Proximity to a polar region with significant quantities of ice, and a region with some notable geothermal activity. Upon landing at a satisfactory site, the robots would set about constructing the habitat. Robot1 would be tasked with boring three large cylinders into the martian landscape; these cylinders would be about twenty feet across, and ten feet deep. These recesses will form the superstructure of the three rooms of our habitat. This format was chosen, because, by lowering the habitat below the surface, it becomes at once robustly insulated, as well as impervious to wind storms. As this process is taking place, Robot2 will gather a large supply of ice from the nearby ice fields. This ice will be melted down and mixed with our sodium to form sodium hydroxide, and hydrogen. The hydrogen will be captured for short-term power generation, and the sodium hydroxide will be mixed with the ferric oxide from the nearby excavation. A generator will burn our hydrogen fuel to produce electricity, with will in turn be used to electrolyse our chemical mixture to produce pure powdered iron. Robot3 will be disassembling the landing module, reconfiguring it into a set of rails, and an electric furnace and manufacturing setup. Once Robot1 has finished with its first hole, Robot4 will descend into the hole as Robot1 exits it. Robot4 is designed to burrow a narrow tunnel straight down to whatever geothermal hotspot was apparent when choosing the landing site, installing behind it a pair of sectional pipes. Robot4 is designed to remain at the bottom of these exchange pipes, and act as a control valve. This pipe-laying process is the first step in designating this first room as the eventual home of the geothermal steam turbine, or "power plant" of the habitat. (Geothermal has been chosen because dust, dust-storms, and a significant distance form the sun make solar power impractical. Wind generation is not necessarily consistent or reliable, and would risk breaking down in the strong martian winds. Geothermal is constant, low-maintenance, and highly reliable). As Robot1 starts on the second cylinder, Robot2 will gather a second load of ice. Robot3 will unpack and install the steam turbine atop the geothermal piping, and when Robot2 returns, water will be fed into the system to initiate closed-cycle steam generation, and bring on-site power online. Robot3 will connect the factory setup to the power supply, as Robot2 loads the iron powder into it, for melting. Robot3 will boil a mixture of water, potassium nitrate, and sodium hydroxide to create a chemical sealant to be applied to the iron. At this point Robot5, which is essentially just a nozzle attached to a large robotic crane arm, would begin extruding the molten iron, like a 3d-printer, across the surface of an inflatable dome-mold, to create the roof-caps of our three rooms. each cap has a circular hole in the top of it where a hatch will be installed a bit later. Once the domes are moulded, Robot3 will apply a coat of sealant to each one, while Robot2 lays sections of railing across our newly dug holes. This railing will be used after the second rocket has arrived, as support as the domes are slid across the open holes to form subterranean (or sub-martian, as the case may be) rooms. Robot1 will then burrow connecting tunnels between the three rooms, and the superstructure of our habitat will be complete! In Phase 2, a second rocket will contain the team of scientists, dehydrated food supplies, lab equipment, and furnishings for the RMH. Once the team has landed, they will go about finishing the interiors of the habitat. Of the three rooms, only the power plant is already complete. The team will drop an inflatable lining into the other two rooms, one of which will become the laboratory, the other of which will become the living quarters. Bunks, dining facilities, lab equipment, and bio-waste recycling equipment will be installed into the habitat, and power will be routed throughout. Doors and hatches will be installed next, and finally, the domes will be slid into place, and the habitat will be complete, and ready to live in. Sodium hydroxide produced during Phase 1 will be integrated into the air scrubbers, also generating a supply of sodium bicarbonate to be used for waste-water filtration. With protection from the elements
Comments